The client is a major player in the European bus industry, with a strong focus on the development and production of a wide range of buses, coaches, and chassis modules. The client’s products are highly regarded for their quality, reliability, and innovative design, making it a preferred choice for customers across more than 30 countries. The client’s project involved a comprehensive redesign of the front interior plastics for an upcoming double-decker coach variant. To achieve this, a collaborative effort was required from all stakeholders, including the customer, offshore and onsite design teams, styling studio, and supplier. The project’s success relied on the timely completion of all plastic component designs, with adherence to strict project timelines. The implementation of a suitable assembly sequence through the design phase resulted in a significant reduction of assembly time by approximately 14%. Furthermore, the manufacturing cost for the newly designed variant was reduced by approximately 6%, when compared to other variants in the same Coach Category. This outcome was achieved through the optimization of the design process, where the TAAL Tech team focused on reducing the number of parts, simplifying the assembly process, and improving the fit and finish of the final product. These measures helped to streamline the production process, resulting in higher efficiency and cost savings, ultimately leading to greater profitability for the client. About Our Client
Business Challenges
Results Delivered
Want to learn more about this engagement?
Download the full case study
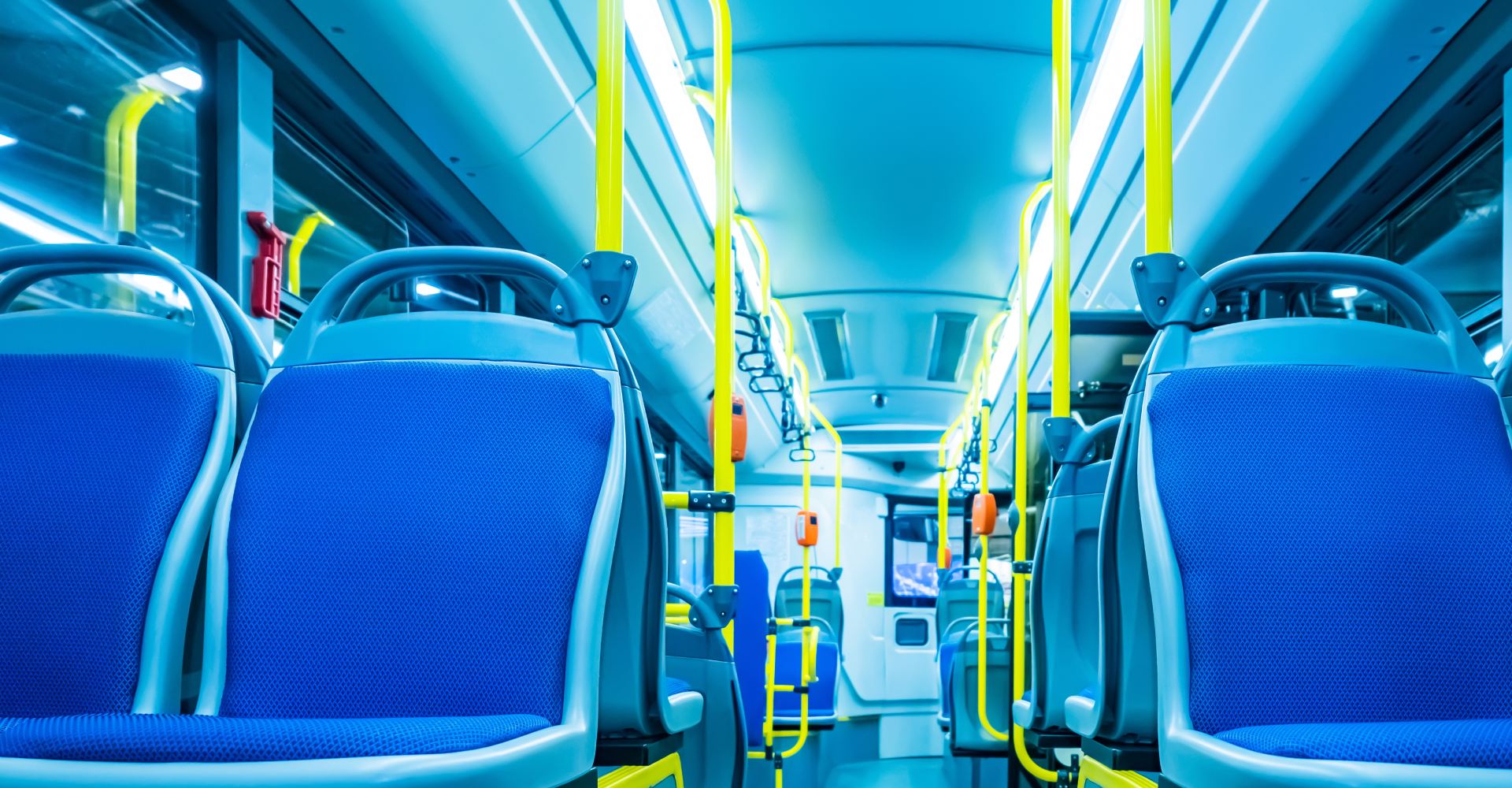