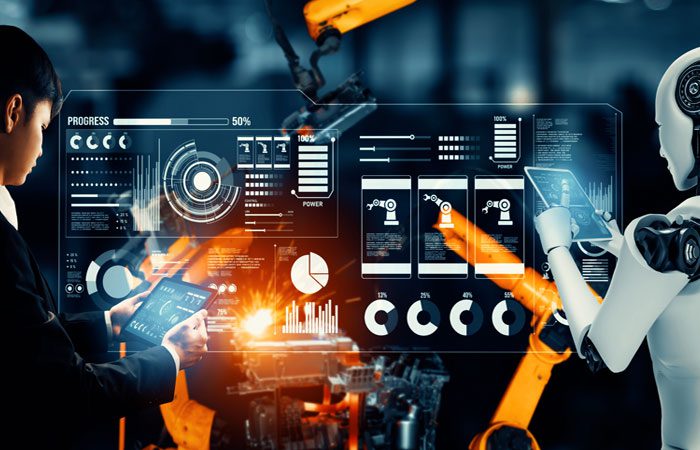
Uncovering the Role of AI and Machine Learning in IIoT Optimization
In modern manufacturing, the integration of Artificial Intelligence (AI) and Machine Learning (ML) into Industrial Internet of Things (IIoT) services is proving to be a revolutionary force. This convergence of technologies is not just a buzzword but a transformative leap that is reshaping manufacturing processes, enhancing predictive maintenance strategies, and elevating the standards of quality control.
In this piece, we will delve into the profound impact of AI and ML on IIoT, exploring the ways in which they are optimizing manufacturing in the 21st century.
- Real-time Optimization of Manufacturing Processes
One of the key contributions of AI and ML in IIoT is their ability to enable real-time optimization of manufacturing processes. Traditional manufacturing setups often grappled with inefficiencies and delays due to manual oversight. However, with the integration of AI-driven analytics, manufacturers can now gain valuable insights into their operations instantaneously.
AI algorithms analyze vast amounts of data generated by sensors and devices on the factory floor, identifying patterns and anomalies that might go unnoticed by human operators. This real-time analysis allows for quick decision-making, optimization of workflows, and minimization of downtime. For instance, AI can predict when equipment is likely to fail, prompting proactive maintenance measures to avoid disruptions in production.
- Predictive Maintenance Redefined
Predictive maintenance has long been a goal for manufacturers seeking to minimize downtime and extend the lifespan of equipment. AI and ML algorithms have redefined the landscape of predictive maintenance within IIoT services. Instead of relying on fixed schedules or reactive measures, these technologies empower manufacturers to predict equipment failures with unprecedented accuracy.
Machine learning models can analyze historical data to identify patterns leading to breakdowns or malfunctions. By continuously learning and adapting, these models become more accurate over time, allowing for precise predictions of when maintenance is required. This shift from preventive to predictive maintenance not only optimizes the use of resources but also contributes to substantial cost savings for manufacturers.
- Quality Control at Unprecedented Levels
Ensuring product quality is paramount in manufacturing, and AI and ML algorithms are playing a pivotal role in enhancing quality control processes. Traditional quality control methods often involved manual inspections, which were time-consuming and prone to human error. With the integration of AI and ML in IIoT, quality control is becoming more precise, efficient, and automated.
Computer vision, a subset of AI, enables machines to ‘see’ and interpret visual data. This technology can be employed in quality control to inspect products for defects, deviations, or variations in real-time. ML algorithms can learn from these inspections, continually improving their accuracy and efficiency. This not only enhances the overall quality of products but also reduces waste and ensures compliance with industry standards.
- Optimizing Resource Utilization
AI and ML are adept at optimizing resource utilization, a critical aspect of manufacturing efficiency. These technologies can analyze data on energy consumption, raw material usage, and production outputs to identify areas for improvement. By optimizing resource utilization, manufacturers can reduce costs, minimize environmental impact, and operate more sustainably.
For instance, AI algorithms can dynamically adjust production schedules based on energy demand patterns, ensuring that machines operate during periods of lower energy costs. Additionally, ML models can optimize the mix of raw materials used in manufacturing processes, reducing waste, and enhancing overall resource efficiency.
- Adaptive Manufacturing in the Industry 4.0 Era
The integration of AI and ML into IIoT services is a cornerstone of the Industry 4.0 revolution. Industry 4.0 represents the fourth industrial revolution, characterized by the fusion of digital technologies, the physical world, and human intelligence. AI and ML are the driving forces behind the adaptability and connectivity that define Industry 4.0.
Through adaptive manufacturing, AI and ML enable factories to respond dynamically to changes in demand, market conditions, and production requirements. Smart factories equipped with AI-powered systems can self-optimize, self-diagnose, and self-correct, creating a more agile and responsive manufacturing ecosystem.
Thus, the integration of AI and ML into IIoT services is propelling manufacturing into a new era of efficiency, reliability, and innovation. The real-time optimization of processes, redefined predictive maintenance strategies, precise quality control measures, resource utilization optimization, and the realization of adaptive manufacturing principles all contribute to a manufacturing landscape that is smarter, more resilient, and ready for the challenges of the future.
As manufacturers embrace the transformative potential of AI and ML in IIoT, they not only unlock new levels of operational excellence but also position themselves at the forefront of technological innovation. The journey towards fully realizing the benefits of these technologies is ongoing, and as we continue to witness advancements, the manufacturing sector is poised for unprecedented growth and competitiveness in the global market. The future of manufacturing is intelligent, adaptive, and powered by the seamless integration of AI and ML into the fabric of Industrial Internet of Things services.