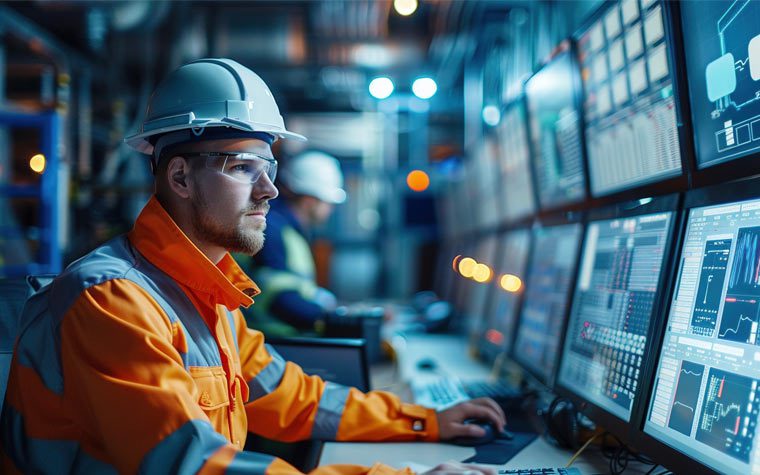
Key Trends in Process Automation for Plant Engineering
The world of plant engineering has seen a significant transformation over the past few years, driven by the need for greater efficiency, safety, and sustainability. At the heart of this evolution is process automation, which is reshaping how industrial plants operate. The deployment of cutting-edge automation technologies helps minimize human intervention in repetitive tasks, increases production accuracy, and improves overall productivity.
As industries embrace the future of manufacturing, it’s critical to understand the trends shaping process automation in plant engineering.
This blog delves into the key trends in process automation, focusing on technologies, strategies, and innovations driving these changes.
- Integration of Industrial IoT (IIoT) for Real-Time Data Insights
One of the most transformative trends in plant engineering is the integration of the Industrial Internet of Things (IIoT). IIoT connects devices, sensors, and machinery, enabling them to communicate with each other and collect vast amounts of real-time data.
Key Advantages:
- Real-time Monitoring: IIoT allows plant operators to monitor equipment performance, energy consumption, and production output in real-time. This leads to better decision-making and improved response times.
- Predictive Maintenance: Sensors embedded in machinery continuously send data to a central system, predicting when maintenance is needed before equipment failure occurs.
- Process Optimization: By leveraging IIoT, plant engineers can use data analytics to identify bottlenecks in the production process, leading to optimized workflows and reduced downtime.
IIoT enables plants to transition from reactive to proactive management, a critical shift in improving efficiency and reducing operational costs.
- Advanced Robotics and AI-Driven Automation
Robotics and artificial intelligence (AI) are at the forefront of modern process automation in plant engineering. With robots handling repetitive or dangerous tasks and AI optimizing workflows, plants are becoming smarter and more efficient.
Key Applications:
- Automated Material Handling: Robots equipped with advanced AI algorithms can move, sort, and process raw materials with precision and speed, reducing human error and increasing productivity.
- Quality Control: AI-powered inspection systems can detect defects in products at a microscopic level, ensuring higher quality standards and reducing waste.
- Collaborative Robotics (Cobots): These robots work alongside human operators, handling strenuous tasks while humans focus on high-level decision-making. Cobots are becoming essential in plant engineering, especially in hazardous environments.
As AI continues to evolve, plants will benefit from faster decision-making, improved safety, and the ability to operate autonomously in dynamic conditions.
- Cloud-Based Automation Platforms
With the rise of digital transformation in industrial operations, cloud computing has become a critical component of process automation. Cloud-based automation platforms enable plants to store and analyze large amounts of data while providing remote access to critical systems.
Benefits:
- Scalability: Cloud solutions can easily scale to meet the needs of growing plants, providing flexibility without the need for costly infrastructure upgrades.
- Remote Monitoring and Control: Plant managers can access and control systems from any location, improving response times and enhancing collaboration among global teams.
- Data Storage and Analytics: Cloud platforms offer virtually unlimited storage capacity, allowing engineers to analyze historical data and gain insights that drive continuous improvement in plant processes.
Cloud-based automation platforms have enabled a shift towards smart manufacturing, where plants are more agile, scalable, and able to adapt to changing market demands.
- Digital Twin Technology for Simulation and Optimization
One of the most innovative advancements in process automation is the use of digital twin technology. A digital twin is a virtual replica of a physical asset, system, or process. By creating a digital representation of a plant or machine, engineers can simulate various scenarios, predict outcomes, and optimize performance.
Key Benefits:
- Risk Mitigation: Digital twins allow plant operators to simulate equipment failures, process changes, and system upgrades without risking real-world disruption.
- Process Optimization: Engineers can test different variables (e.g., temperature, pressure) within the digital twin to identify optimal conditions for production.
- Predictive Maintenance and Performance: Digital twins continuously monitor equipment performance, comparing real-time data with the virtual model to identify potential issues and suggest corrective actions.
Digital twin technology enables plant engineers to refine operations without interrupting production, ultimately improving operational efficiency and reducing maintenance costs.
- Enhanced Cybersecurity for Automated Systems
With the increasing integration of digital tools in process automation, the risk of cyberattacks has grown significantly. Plant operations are now vulnerable to hacking, ransomware, and other cyber threats that can disrupt production and compromise sensitive data.
Cybersecurity Measures:
- Secure Network Architectures: Plants are adopting more secure network designs to safeguard their automated systems from unauthorized access.
- AI-Driven Threat Detection: AI and machine learning are being used to identify and neutralize potential threats before they impact plant operations.
- Data Encryption and Multi-Factor Authentication: These measures ensure that only authorized personnel have access to critical systems and sensitive data.
As more plants move towards fully automated systems, strengthening cybersecurity protocols is paramount to safeguarding operations and protecting against potentially devastating attacks.
- Edge Computing for Faster Data Processing
While cloud computing has brought significant advantages to plant automation, edge computing is gaining momentum for its ability to process data closer to the source—at the edge of the network. In plant engineering, this means that critical data can be analyzed in real-time, without the latency associated with cloud-based processing.
Advantages of Edge Computing:
- Low Latency: Real-time data processing at the source allows plants to respond faster to system anomalies and changes in production conditions.
- Improved Reliability: By reducing reliance on centralized cloud infrastructure, edge computing minimizes the risk of downtime caused by network outages.
- Cost Efficiency: Edge computing reduces bandwidth usage and storage costs by processing data locally, sending only relevant information to the cloud.
Edge computing is becoming essential in industries that require rapid decision-making and real-time data analysis, such as oil and gas, chemical plants, and manufacturing.
- Autonomous Systems and Self-Learning Machines
Autonomous systems powered by machine learning are gradually taking over complex operations in plant engineering. These self-learning systems can adjust processes on their own based on real-time conditions, minimizing the need for human intervention.
Key Benefits:
- Autonomous Control Systems: Automated systems can adapt to changes in production variables without the need for manual adjustments, leading to improved precision and efficiency.
- Self-Optimization: Self-learning machines can identify inefficiencies and continuously optimize operations, driving improvements over time.
- Reduced Human Error: By delegating complex tasks to autonomous systems, plants can reduce the risk of errors caused by human oversight, leading to safer and more reliable operations.
As autonomous technologies continue to mature, plant engineers will be able to operate complex systems with greater confidence and efficiency.
- How an Engineering Services Company Can Help
The successful implementation of process automation technologies in plant engineering requires not only advanced tools but also skilled expertise. Engineering services companies play a critical role in facilitating the transition to automation by offering the following:
- System Integration: Engineering firms can integrate diverse automation systems, ensuring seamless communication between machines, sensors, and control systems.
- Consulting and Strategy: Experienced engineers can provide strategic insights into how process automation can be customized to meet the specific needs of a plant.
- Training and Support: Engineering firms offer training to plant operators, ensuring that teams are fully equipped to leverage the latest automation technologies effectively.
Partnering with an engineering services company enables plant managers to unlock the full potential of process automation, driving innovation, efficiency, and profitability.
As process automation continues to advance, the benefits for plant engineering are undeniable. From IIoT integration to autonomous systems, the adoption of these technologies is leading to safer, more efficient, and cost-effective operations. By staying up-to-date with the latest trends and collaborating with engineering services experts, plants can stay ahead of the curve and thrive in the digital age.