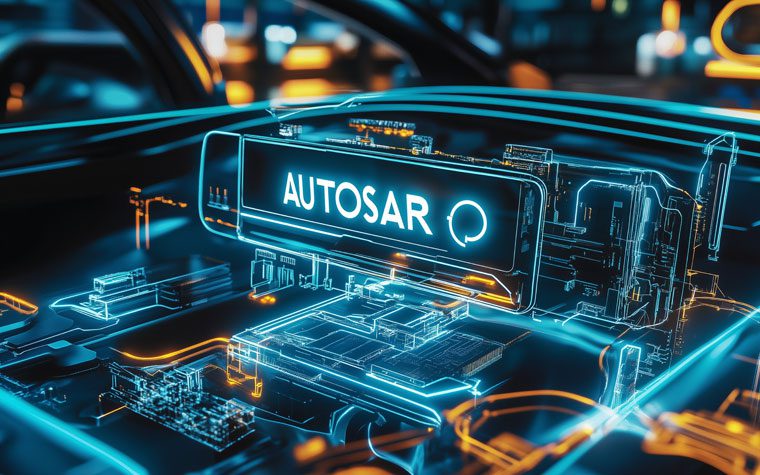
AUTOSAR vs. Non-AUTOSAR: What’s the Best Choice for Future Vehicle Architectures?
With the rapid evolution of automotive technology, software is now a defining element of vehicle architecture. To standardize and streamline automotive software development, AUTOSAR (AUTomotive Open System ARchitecture) emerged as a global standard. However, Non-AUTOSAR solutions also remain prevalent, offering flexibility and customization.
So, which is the better choice for future vehicle architectures?
This blog delves into the pros, cons, and best use cases of AUTOSAR and Non-AUTOSAR approaches to help automakers and engineers make informed decisions.
Understanding AUTOSAR and Non-AUTOSAR
What is AUTOSAR?
AUTOSAR is a standardized framework for automotive embedded software development. It defines a common software architecture that enables seamless integration, interoperability, and reusability across different Electronic Control Units (ECUs).
Key Features of AUTOSAR:
- Layered Software Architecture (separates application, services, and hardware abstraction layers)
- Standardized Interfaces (enables component interoperability)
- Scalability (suitable for various vehicle segments, from economy cars to luxury models)
- Safety and Security Compliance (supports ISO 26262 functional safety requirements)
- Reusability (software components can be reused across different ECUs and OEMs)
What is Non-AUTOSAR?
Non-AUTOSAR refers to proprietary or custom-developed software architectures that do not follow AUTOSAR standards. These architectures are typically used for specialized applications, offering greater flexibility and efficiency in certain scenarios.
Key Features of Non-AUTOSAR Solutions:
- High Customization (tailored solutions for specific use cases)
- Optimized Performance (minimal overhead compared to standardized frameworks)
- Faster Development Cycles (no dependency on compliance with AUTOSAR regulations)
- Greater Control (OEMs and Tier 1 suppliers have full authority over software design)
Key Differences Between AUTOSAR and Non-AUTOSAR
Feature | AUTOSAR | Non-AUTOSAR |
Standardization | Yes, globally accepted | No, proprietary or custom |
Development Time | Longer (due to compliance requirements) | Shorter (more agile development) |
Reusability | High (software components reusable across projects) | Low (custom solutions for specific needs) |
Scalability | Designed for scalability across vehicle segments | Limited to specific projects |
Cost | Higher initial cost due to licensing and integration | Lower initial cost but may increase with complexity |
Flexibility | Less flexible (strict standard compliance) | Highly flexible (tailored to exact requirements) |
Cybersecurity | Robust, standardized security mechanisms | Requires custom security solutions |
Functional Safety | Compliant with ISO 26262 | Custom implementation needed |
Pros and Cons of AUTOSAR and Non-AUTOSAR
Advantages of AUTOSAR
- Standardized Development: Simplifies integration across multiple ECUs and OEMs.
- Interoperability: Facilitates communication between different software components and suppliers.
- Safety & Security Compliance: Supports regulatory requirements, making it ideal for safety-critical applications.
- Future-Proofing: Ensures compatibility with evolving automotive technologies.
Challenges of AUTOSAR
- Complex Implementation: Requires expertise and compliance with strict regulations.
- Higher Costs: Licensing, integration, and maintenance costs can be significant.
- Inflexibility for Custom Applications: May not be ideal for niche or experimental vehicle functions.
Advantages of Non-AUTOSAR
- Greater Customization: Allows automakers to develop unique features tailored to their needs.
- Optimized Performance: No additional overhead from standardization layers.
- Faster Time-to-Market: Agile development cycles with minimal compliance constraints.
- Cost Efficiency for Niche Applications: Lower initial investment for startups and small-scale projects.
Challenges of Non-AUTOSAR
- Lack of Standardization: Integration with third-party components can be difficult.
- Security Risks: Requires custom security measures, which may not be as robust as AUTOSAR.
- Limited Reusability: Custom solutions are often project-specific, increasing long-term development costs.
Which One is Best for Future Vehicle Architectures?
When to Choose AUTOSAR?
For OEMs and Tier 1 Suppliers: If you are a large automaker or supplier dealing with complex vehicle ecosystems, AUTOSAR provides a standardized, scalable, and interoperable software framework.
For Safety-Critical Applications: Vehicles with Advanced Driver Assistance Systems (ADAS), Functional Safety (ISO 26262), and Autonomous Driving require the structured compliance that AUTOSAR provides.
For Long-Term Development & Compatibility: If you plan to scale your vehicle software across multiple models and future generations, AUTOSAR ensures reusability and future-proofing.
When to Choose Non-AUTOSAR?
For Startups and Small-Scale Projects: If you are developing a niche automotive application with specific performance and cost constraints, a custom Non-AUTOSAR approach allows more control.
For High-Performance or Experimental Applications: If your project requires ultra-optimized embedded systems (e.g., motorsports, specialized electric drivetrains, or innovative HMI solutions), Non-AUTOSAR offers unmatched flexibility.
For Faster Prototyping: If you need to bring a product to market quickly, avoiding the overhead of AUTOSAR compliance may accelerate development.
Finding the Right Balance
There is no one-size-fits-all approach when choosing between AUTOSAR and Non-AUTOSAR. The right choice depends on project scale, regulatory requirements, and long-term goals.
- AUTOSAR is best for scalable, safety-critical, and standardized vehicle architectures.
- Non-AUTOSAR is ideal for high-performance, cost-sensitive, or niche applications requiring deep customization.
For many OEMs, a hybrid approach that blends both AUTOSAR and custom software solutions may be the most effective strategy for building the next generation of vehicles.