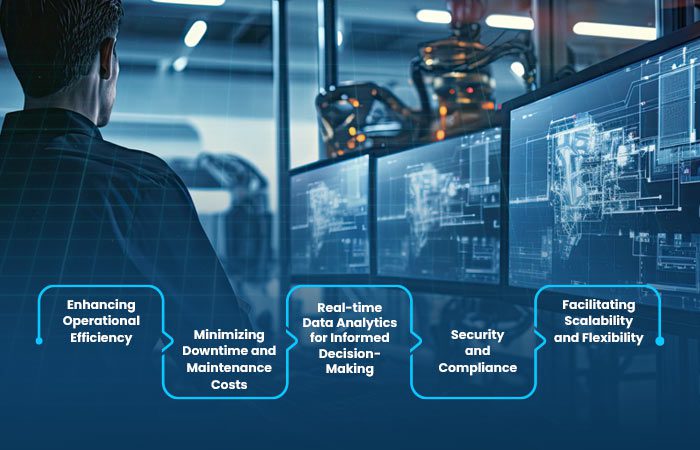
Why is Remote Device Management for Manufacturing a Gamechanger?
In the rapidly evolving landscape of modern manufacturing, the integration of technology has become more critical than ever before. One of the key pillars supporting this technological transformation is remote device management. In a world where connectivity and efficiency are paramount, the ability to monitor and control manufacturing devices remotely has become a game-changer for businesses. In this blog post, we’ll delve into the importance of remote device management for manufacturing and explore how it contributes to increased efficiency, cost-effectiveness, and overall operational excellence.
- Enhancing Operational Efficiency
Manufacturing processes involve a myriad of interconnected devices and machinery. From automated assembly lines to sophisticated robotics, the modern factory floor is a complex ecosystem of technology. Remote device management allows manufacturers to monitor and control these devices from a centralized location, irrespective of geographical distances. This capability enhances operational efficiency by providing real-time insights into the status of equipment, production rates, and potential issues.
Consider a scenario where a manufacturing facility operates 24/7. With remote device management, production managers can access and analyze data even outside regular working hours. This not only facilitates quick decision-making but also enables proactive problem-solving. Identifying and addressing issues remotely minimizes downtime and ensures that the production line keeps running smoothly. The advantage of this remote intervention capability is twofold: it elevates overall productivity and enhances the adaptability of the manufacturing process.
- Minimizing Downtime and Maintenance Costs
In the manufacturing industry, minimizing downtime is crucial for upholding productivity. Every minute a production line is halted can result in significant financial losses. Remote device management plays a crucial role in minimizing downtime by allowing technicians to diagnose and address issues without being physically present on the factory floor.
Through remote monitoring, maintenance teams can detect potential problems before they escalate, enabling preventive measures to be taken. This proactive approach not only reduces the frequency and duration of downtime but also cuts down on maintenance costs. Predictive and Proactive maintenance, facilitated through remote device management, ensures that machinery receives service and repairs precisely when needed. This strategy is key in averting sudden malfunctions and the associated expensive urgent fixes.
- Real-time Data Analytics for Informed Decision-Making
In the manufacturing sector, data is paramount. Remote device management enables the monitoring of real-time data from a multitude of devices throughout the factory floor.
This data can be analyzed to gain insights into production processes, equipment performance, and overall efficiency. Armed with this information, manufacturers can make informed decisions to optimize production, reduce waste, and enhance quality.
For example, monitoring data on the energy consumption of machinery can help identify opportunities for energy savings. Analyzing production rates and error rates in real-time allows for adjustments to be made swiftly, ensuring that resources are utilized efficiently. The ability to gather and analyze data remotely empowers manufacturing leaders to make data-driven decisions that contribute to the overall success of the business.
- Security and Compliance
In an era where cyber threats are ever-present, ensuring the security of manufacturing systems is paramount. Remote device management systems often include robust security measures to protect sensitive data and prevent unauthorized access. Manufacturers can implement encryption, multi-factor authentication, and other security protocols to safeguard their operations.
Moreover, compliance with industry regulations and standards is a top priority for manufacturing companies. Remote device management facilitates adherence to these regulations by providing tools to monitor and audit processes remotely. This not only ensures compliance but also simplifies the process of preparing for inspections and certifications.
- Facilitating Scalability and Flexibility
As manufacturing businesses grow, the need for scalability and flexibility becomes increasingly important. Remote device management systems are designed to scale with the growing demands of a business. Whether it’s expanding production capacity or integrating new technologies, the ability to remotely manage devices streamlines the process and reduces the logistical challenges associated with scaling up operations.
Furthermore, remote management enhances the flexibility of manufacturing operations. With the ability to monitor and control devices from anywhere with an internet connection, manufacturers can adapt to changes in demand, supply chain disruptions, or unforeseen circumstances. This flexibility is a valuable asset in an environment where agility and responsiveness are key to success.
Thus, remote device management has emerged as a cornerstone of modern manufacturing. Its impact on operational efficiency, cost-effectiveness, and overall productivity cannot be overstated. As manufacturing processes continue to evolve and become increasingly complex, the ability to monitor and control devices remotely provides a competitive edge in the industry.
Manufacturers who invest in robust remote device management systems position themselves to navigate the challenges of the digital age successfully. From minimizing downtime and maintenance costs to harnessing the power of real-time data analytics, the benefits of remote device management extend across various facets of manufacturing operations. Embracing this technology is not just a matter of convenience; it is a strategic imperative for businesses aiming to thrive in the dynamic and competitive landscape of modern manufacturing.