Unleash the power of strategic plant layouts
Layout engineering is a crucial aspect of the overall engineering design process for industrial facilities. It involves planning and organizing the physical arrangement of equipment, structures, and systems within a plant to optimize functionality, safety, and efficiency. From conceptualization to execution, our services encompass space utilization, equipment positioning, and infrastructure planning, ensuring a harmonized and ergonomic environment.
At TAAL Tech, our Layout Design Engineering is focused on Petroleum Refineries and Refinery Units, Tank Farms, Chemical plants, and Terminals.
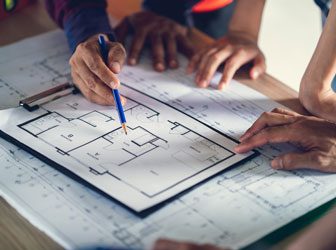
Site Planning
Assess the available site space and topography to determine the optimal location for the facility. Plan for future expansion and consider factors such as access to transportation, utilities, and environmental considerations.
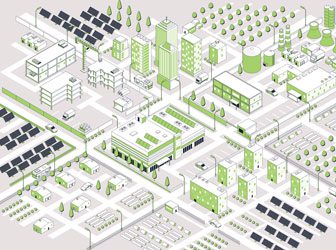
Equipment Layout
Develop detailed equipment layouts, considering process flow, operational requirements, and safety concerns. Optimize the arrangement of major equipment to minimize material handling distances and improve operational efficiency.
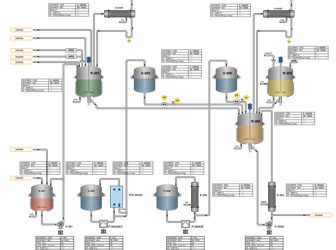
Piping and Instrumentation Diagrams (P&ID)
Translate the process design into detailed P&IDs that show the interconnection of equipment and the flow of materials. Use P&IDs to inform the layout of piping systems, ensuring efficient and safe material transfer.
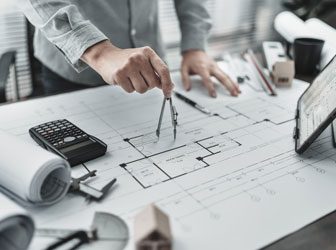
Spatial Arrangement
Considering factors such as clearances, access ways, and operational ergonomics when arranging equipment and structures. Ensuring that sufficient space is available for maintenance activities and the safe movement of personnel.
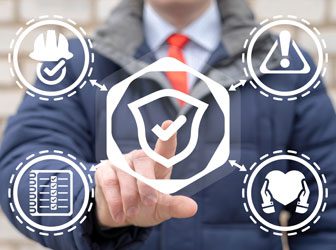
Safety and Regulatory Compliance
Design layouts that comply with safety standards and regulations, including considerations for fire safety, emergency exits, and hazardous material storage. Implement safety zones and barriers to prevent accidents and protect personnel.
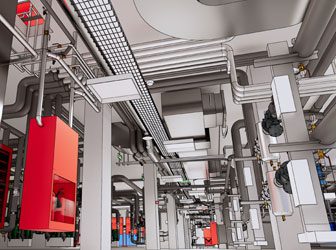
Utilities Planning
Design the layout of utility systems, including water supply, steam generation, power distribution, and HVAC (heating, ventilation, and air conditioning). Ensure efficient routing of utility lines to support the various processes within the facility.
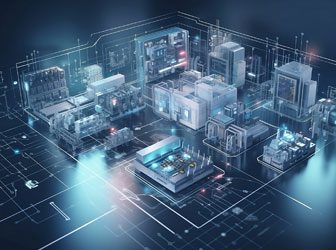
Scalability
Design layouts that allow for modularity and flexibility to accommodate changes in production processes or future expansion. Considering the use of standardized equipment and modular units to enhance flexibility.
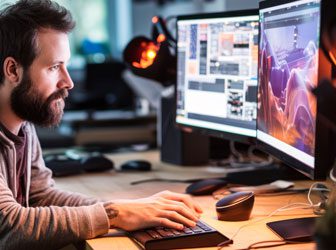
Technology Intervention
Utilize 3D modelling software to create virtual representations of the facility layout. Conduct virtual walkthroughs to identify potential clashes or issues before construction begins.
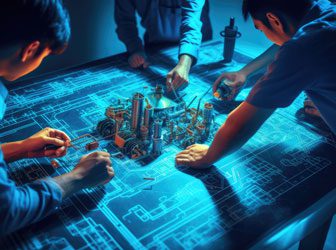
Cross-Collaboration
Internal collaboration with process engineering team to ensure alignment between process design and equipment layout. Engaging with client to understand specific layout requirements and preferences and feedback to meet their operational needs.
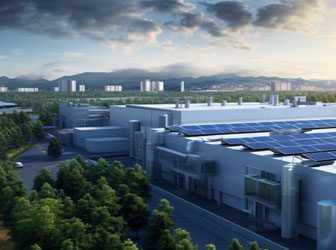
Sustainability
Consider environmental factors in the layout design, such as noise control, emissions dispersion, and landscaping for aesthetic and ecological purposes.
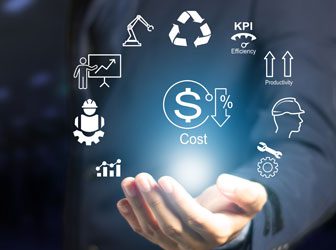
Cost & Efficiency
Considering cost implications related to equipment placement, utility routing, and construction logistics. Optimizing layout designs to minimize construction costs and improve overall project economics by leveraging advanced technologies, such as automation and digital monitoring.
Technologies
Aspen HYSYS
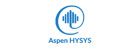
CADWorx
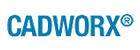
AutoCAD Plant 3D
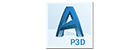
E3D
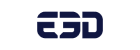
SmartPlant-PID
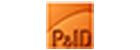
AutoCAD
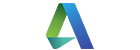
CAESAR II
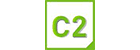
AutoPIPE
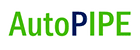
STAAD.Pro
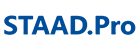
AutoPLANT
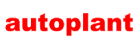
Tekla
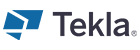
ETAP
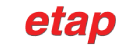