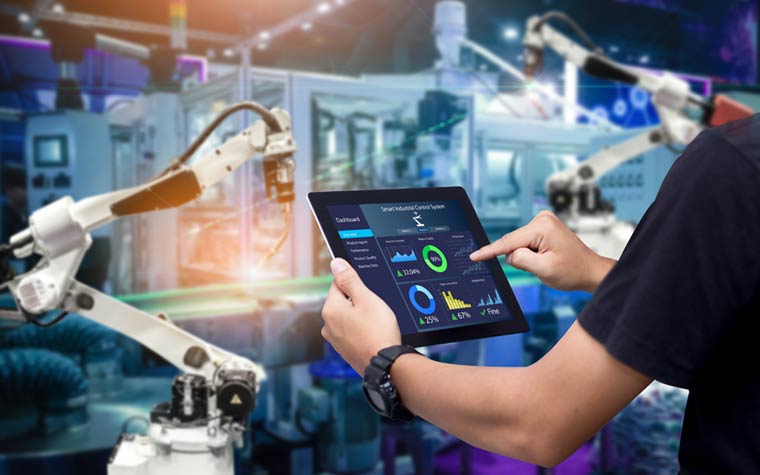
The Role of IIoT in Reducing Downtime Through Real-Time Condition Monitoring
Maximizing productivity and minimizing downtime are crucial for staying competitive in the industrial landscape today. Downtime, whether planned or unplanned, can significantly impact profitability and disrupt workflow. Traditionally, industries relied on periodic maintenance schedules, which often led to over-maintenance or unexpected breakdowns.
However, the Industrial Internet of Things (IIoT) has emerged as a game-changer by enabling real-time condition monitoring, which helps industries to predict, prevent, and minimize downtime. Keep reading this blog to know more!
Understanding Condition Monitoring and Its Importance in Industry
Condition monitoring involves tracking the health of machinery and equipment to identify signs of wear and tear, misalignment, or other potential issues. Traditionally, maintenance was reactive—addressing breakdowns as they occurred—or scheduled at regular intervals without regard to the equipment’s actual condition.
IIoT has revolutionized this by enabling predictive and prescriptive maintenance. Through real-time condition monitoring, IIoT provides immediate insights into equipment health, helping industries to maintain uptime, optimize maintenance schedules, and extend asset life.
How Does IIoT Power Real-Time Condition Monitoring?
- Real-Time Data Collection from Sensors
The foundation of real-time condition monitoring lies in data collection. IIoT enables the integration of smart sensors that continuously monitor various parameters, including temperature, vibration, humidity, pressure, and more.
These sensors collect data on equipment performance and detect even the slightest deviations from the norm. This data is transmitted to central systems for analysis, allowing technicians and operators to monitor conditions in real time.
- Analyzing Data with AI and Machine Learning
IIoT platforms incorporate AI and machine learning (ML) algorithms that analyze vast amounts of data collected by sensors. These algorithms are designed to recognize patterns, flag anomalies, and predict future conditions based on historical data. For instance, if a machine’s vibration pattern deviates from its normal operation, ML algorithms can alert technicians of potential bearing issues well before a failure occurs. This helps industries to move from reactive to predictive maintenance, addressing issues proactively and preventing unexpected downtime.
- Centralized Data Management and Cloud Computing
Real-time condition monitoring generates a massive amount of data, which needs to be efficiently stored, processed, and managed. IIoT leverages cloud computing to handle this data, providing scalable storage and powerful computing resources.
Cloud-based platforms centralize data collection, making it accessible from any location. Operators can monitor equipment across multiple facilities, enabling remote monitoring and ensuring consistency in maintenance practices.
- Edge Computing for Real-Time Insights
While cloud computing is essential for data management, IIoT also uses edge computing to bring data processing closer to the source. Edge devices process data locally, reducing latency and enabling instant insights.
For critical equipment or processes, where immediate response is crucial, edge computing ensures timely alerts and fast action. This is particularly valuable in industries like oil and gas, where delays in responding to equipment failures could lead to hazardous situations.
Benefits of IIoT-Driven Real-Time Condition Monitoring
- Predictive Maintenance and Reduced Downtime
The primary advantage of IIoT in condition monitoring is its predictive maintenance capability. By identifying issues before they escalate, IIoT reduces unplanned downtime. For example, rather than waiting for a motor to fail, IIoT can alert operators when it is showing early signs of overheating or abnormal vibration. Predictive maintenance minimizes costly repairs, prevents production halts, and maximizes machine availability.
- Extended Equipment Lifespan
IIoT’s real-time monitoring allows industries to extend the lifespan of machinery and equipment. Proactive maintenance based on real-time data prevents excessive wear and tear, ensuring assets are maintained in optimal condition. With improved maintenance practices, industries can extend the functional life of equipment, reducing the need for frequent replacements and lowering capital expenditures.
- Cost Savings through Optimized Maintenance
Scheduled maintenance often leads to unnecessary interventions, while reactive maintenance typically incurs higher costs due to urgent repairs. IIoT optimizes maintenance schedules based on equipment condition, reducing maintenance costs. Predictive maintenance also means fewer spare parts, less downtime, and lower labor costs, leading to significant savings.
- Enhanced Safety and Risk Management
IIoT-enabled condition monitoring improves workplace safety by identifying and addressing equipment malfunctions before they pose a hazard. For example, sensors can detect gas leaks, high temperatures, or abnormal pressure in pipelines, alerting personnel to potential dangers. This proactive approach minimizes the risk of accidents, protects workers, and reduces liability.
Industry Applications of IIoT in Condition Monitoring
- Manufacturing
In manufacturing, IIoT is widely used for monitoring critical machinery, including conveyor belts, CNC machines, and injection molding equipment. Condition monitoring enables manufacturers to maintain a steady workflow and avoid costly production delays. For example, automotive plants use IIoT to monitor robotic assembly lines, ensuring seamless production and reducing bottlenecks.
- Oil and Gas
The oil and gas industry relies heavily on IIoT for real-time monitoring of pipelines, rigs, and drilling equipment. With assets spread across remote locations, IIoT sensors provide continuous monitoring, helping to prevent leaks, explosions, and environmental hazards. This improves operational efficiency, enhances safety, and minimizes environmental risks.
- Power Generation and Utilities
IIoT has transformed the energy sector by enabling real-time monitoring of power generation equipment, transformers, and grid infrastructure. In renewable energy, for instance, IIoT monitors wind turbines and solar panels, tracking performance to ensure efficient energy production and reduce maintenance costs.
- Transportation and Logistics
In logistics, IIoT-driven condition monitoring tracks vehicle health, ensuring trucks, trains, and other vehicles are maintained in top condition. Real-time data on engine performance, tire pressure, and brake wear helps prevent breakdowns during transit, ensuring timely deliveries and reducing operational costs.
Key Challenges in Implementing IIoT for Condition Monitoring
- Data Security and Privacy Concerns
IIoT solutions often involve the transmission of sensitive operational data. Securing this data from cyber threats is paramount. Companies need to implement robust security measures, including encryption, multi-factor authentication, and secure network protocols, to protect data integrity and privacy.
- Integration with Legacy Systems
Many industries operate with legacy equipment that lacks built-in connectivity. Integrating IIoT with these systems can be challenging, requiring retrofitting or the use of external sensors. However, solutions like edge devices and IoT gateways can help bridge the gap, making it possible to gather data from older equipment.
- Initial Costs and ROI
Implementing IIoT-based condition monitoring requires investment in sensors, connectivity, and data infrastructure. Although the initial costs can be high, the long-term savings from reduced downtime and optimized maintenance can justify the expense. Companies often perform ROI analysis to evaluate the cost-benefit ratio before implementation.
The Future of IIoT in Condition Monitoring
As IIoT technology continues to evolve, new advancements in AI, machine learning, and connectivity (e.g., 5G) will further enhance condition monitoring. Emerging trends include self-learning algorithms that continuously improve predictive accuracy, advanced edge computing for real-time data processing, and integration with augmented reality for maintenance support.
These advancements will make condition monitoring even more precise, accessible, and integral to industrial operations.
The Industrial Internet of Things has transformed the way industries approach downtime and maintenance. By enabling real-time condition monitoring, IIoT allows companies to move from reactive to predictive maintenance, maximizing uptime, reducing costs, and improving safety. As industries continue to embrace IIoT, the technology will play a critical role in driving efficiency, sustainability, and resilience in the modern industrial ecosystem.